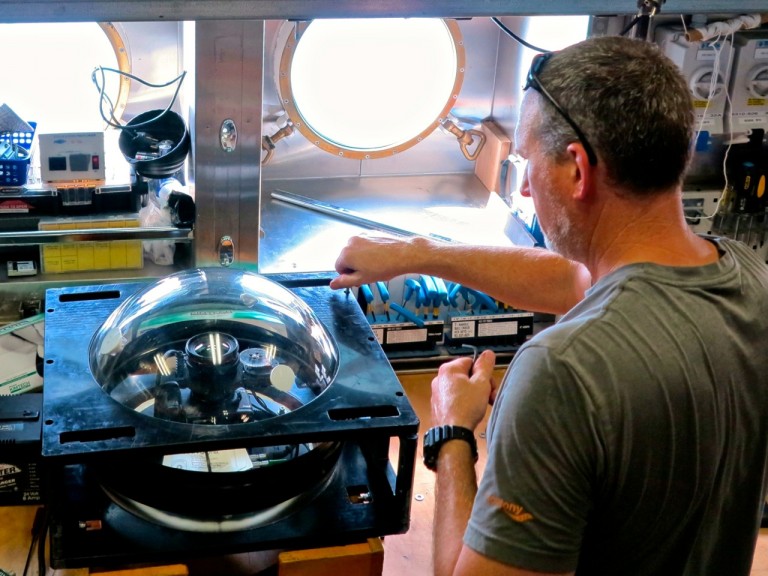
What is a Lander
A lander is a versatile mechanical platform used for carrying tools, instruments, scientific samples, imagery, measurements, etc. between the surface and the bottom of the sea. Picture an underwater elevator with the ground floor almost seven miles below the ocean surface. Landers usually consist of a metal frame shaped like a large square desk with a perforated top and tall mast in the middle that carries lightweight flotation at its top.
Landers are launched into the ocean with attached ballast weights that allow it to free-fall to the bottom. Depending on the depth, the descent to the seafloor could take up to several hours. At the end of each deployment, the ballast weights are released with a timer or acoustic signal and the lighter-than-water lander then ascends to the surface. Once on the surface, the lander’s antennas and bright color of the flotation foam make it easy to spot and recover the lander.
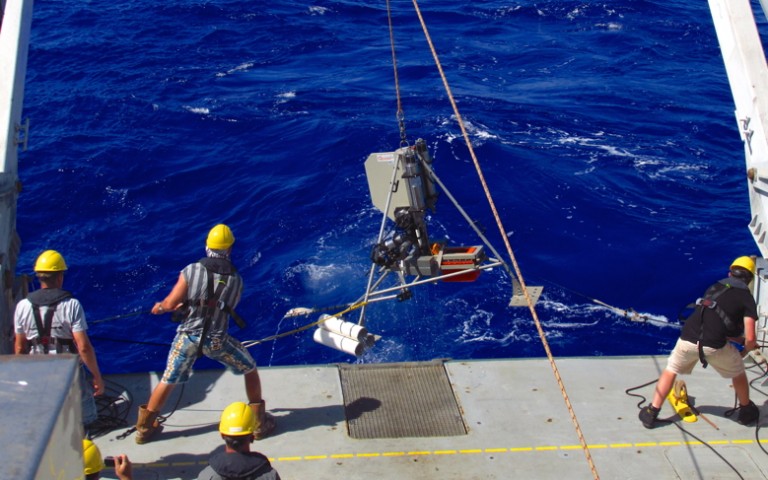
What can landers do?
Landers are designed to be both versatile to accommodate different payloads and are modular to facilitate use of various specialized add-on scientific systems, samplers, and instruments. The lander base platform can be replaced with specialized assembly housing such as coring respirometers. Landers can provide additional payload carrying capacity to remotely operated vehicles (ROVs). This reduces the need to bring an ROV to the surface when it runs out of sample storage and allows the vehicle to spend more time performing useful work on the seafloor, rather than traveling through the water column.
The lander can hold lights and cameras, and can be baited with “food falls” to attract and record different scavenger species at depth. Water samples can also be installed on the landers to collect deep sea water for chemical and microbial analysis.
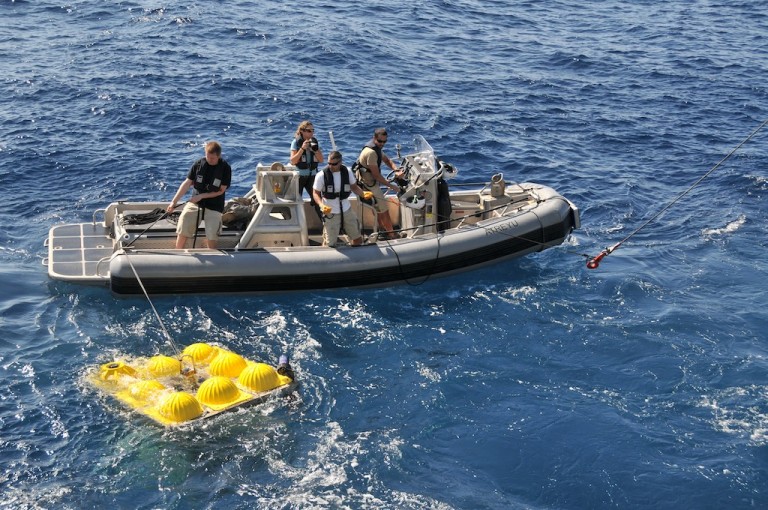
How does a lander float to the surface?
Sending a 225-kilogram (500-pound) instrumented lander to even the deepest portions of the ocean is easy. The challenge is getting it back safely, a feat that requires substantial and reliable buoyancy. To overcome the limitations of conventional deep-sea buoyancy solutions, Schmidt Ocean Institute’s lander depends on a high-tech foam that has already proven itself capable of handling one of the world’s most extreme environments.
When building deep-sea equipment such as landers, engineers have traditionally relied on large, spherical glass floats to provide the buoyancy needed to return systems to the surface after the triggered release of weights. But these floats can fail, particularly with repeated use, and when they do the resulting implosion can cause major damages and even prevent retrieval. To avoid the limitations of conventional glass spheres, the SOI lander gets its buoyancy from a specialized foam made of tiny, hollow glass microspheres embedded in an epoxy resin. The spheres range in size from 10 to 100 microns—so tiny that you need a microscope to see them.